はじめに
皆さんは【品質は工程で造り込む】という言葉をご存知ですか?
かの有名な『TOYOTA』の品質に対する考え方から出てきた言葉ですね♪
『自工程完結』と言われるものです。
詳しくはこちら→wikiよりhttps://ja.m.wikipedia.org/wiki/%E8%87%AA%E5%B7%A5%E7%A8%8B%E5%AE%8C%E7%B5%90
今回はこの『品質は工程で造り込む』について解説していこうと思います!
この記事では
・不具合品や不良品が多過ぎて処理が間に合わない!
・検査員を増員したが、いくら増員しても対応が間に合わない!
・客先からのクレームが次々と後を絶たない!
といった問題を解決するためにどうすれば良いか?
その具体的なアクションについて解説していきたいと思います♪
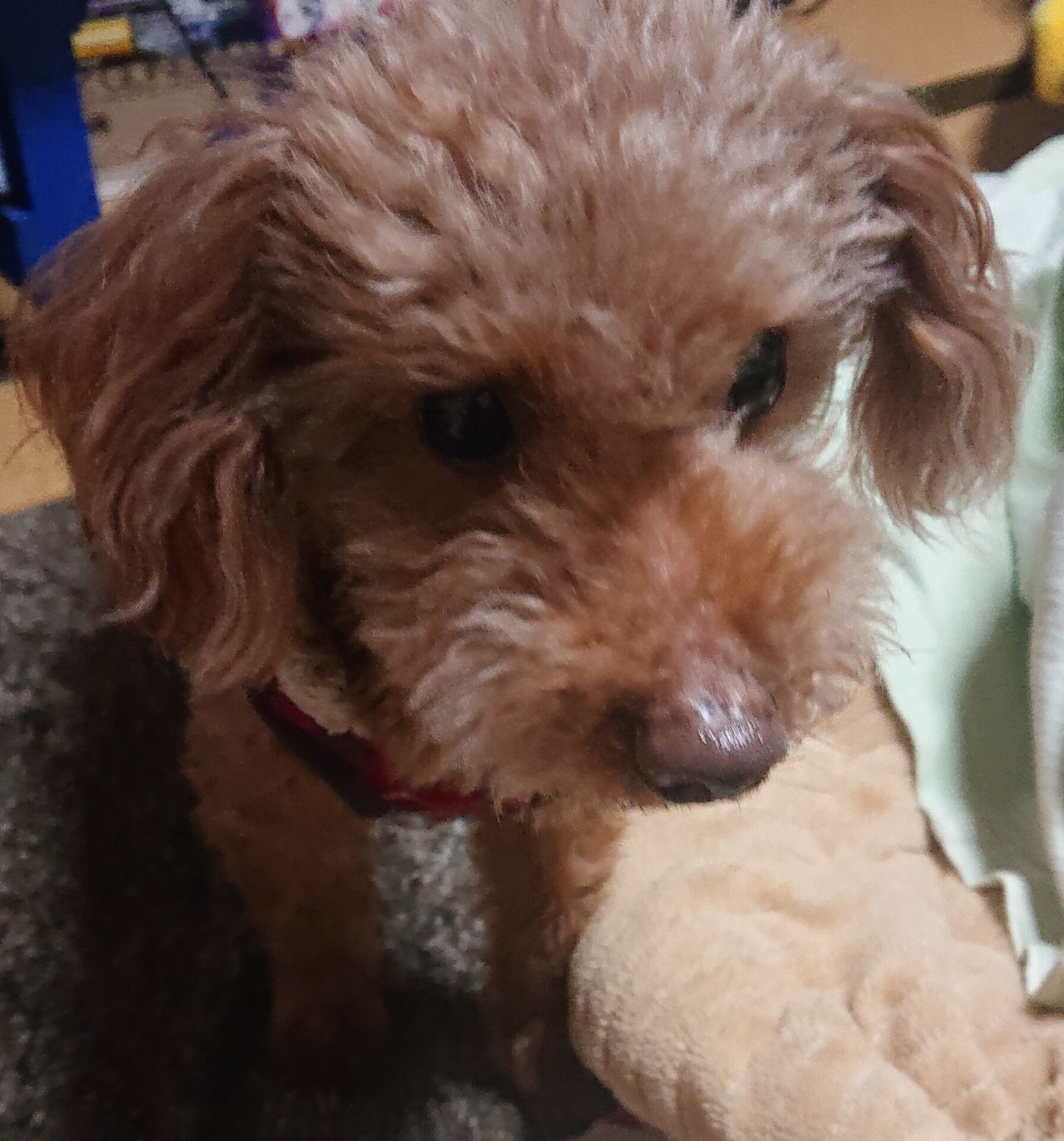
ちなみにこの記事は、10年以上工場勤務をして『現場改善・品質改善』に取り組み、最終的に管理職として組織をマネジメントしてきた経験をもとに書いています。
なぜ『品質を工程で造り込む』必要があるのか?
突然ですが、川の話をします(笑)
下流や河口にゴミが大量にたまって、皆で清掃活動をしたりしてキレイにします。が、またゴミがたまってまた清掃活動をしなくちゃならなくなります。また清掃・・・。
いくら清掃活動してもきりがありません!
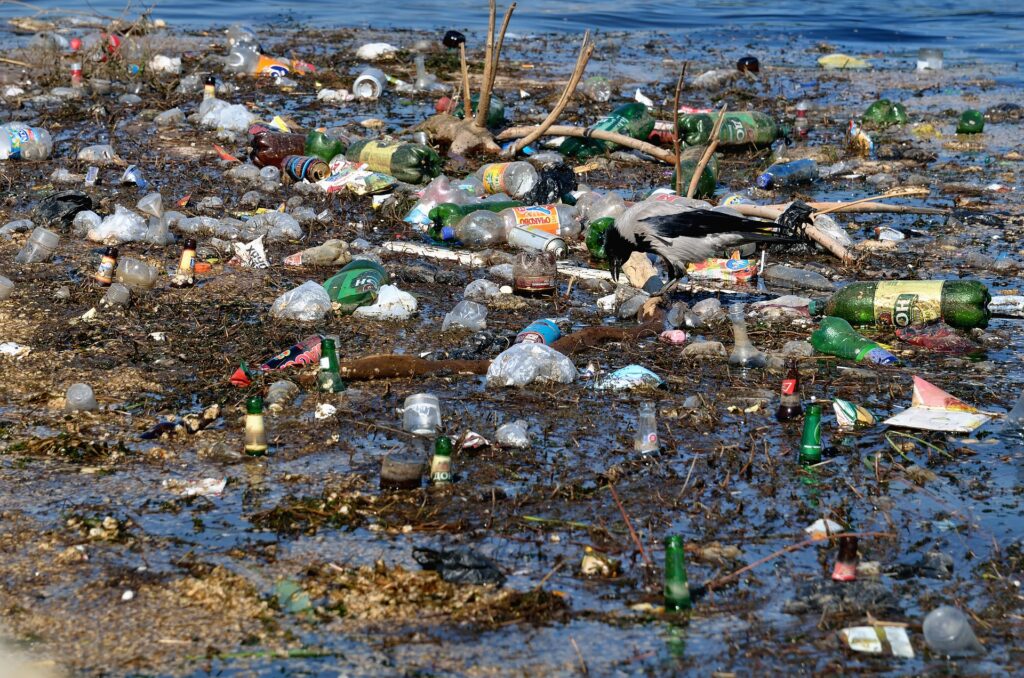
何故なら上流でゴミがどんどん発生しているからです!
これを会社に当てはめると、
上流→製造ライン
下流→検査ライン
海→納入先
という構図になりますね♪
上流からどんどんゴミが流れてきて、下流はゴミだらけ!
処理が間に合わなくて、ゴミが海に流れ出す!
そうなったらクレームの嵐が来るわけです(笑)
何とか対応しようと残業したり、検査員を増員して対応なんて事もありがちですが、ゴテゴテにまわりますし、何より経費をかなり圧迫することになります。
『残業の削減の方法』については、過去に取り上げていますので参考に見て下さい♪
合わせて読みたい→【管理職向け】残業削減の為の3つの方法『序章』
こういった事態が発生しないようするために『工程で品質を造り込む』が必要になるわけですね。
マニュアルだけでは不十分?
製品の出来映えの良し悪しが決まるのは『製造工程』ですね。
『検査工程』で不良品が良品に変わったりはしません!
まぁ、手直しとかして不良品を良品転化する場合は置いといて(・・;)
なので、
製造部門の作業者に「気を付けるように!」何て言っても、そりゃあ作業者も人間です。
忘れる時や、気がつかない時もありますわ!
そこで登場するのが『作業マニュアル』です。
『作業マニュアル』については詳しくは
過去記事→【管理職向け】残業削減の為の3つの方法 第3章『手順・基準編」
にて、手順や基準をどう作成していくか?をまとめていますので参考にしてください♪
マニュアルに落としこんで作業者にそれを徹底してもらう!
そうすれば、不良品の発生はグッと押さえられます(^.^)
が、しかしそれだけでは不十分なんです!
何故不十分なのか?
それは、製造ラインにいる作業者は品質だけでなく『能率に追われている』からです。
マニュアルがあっても作業に追われていると、確認を省いたり「たぶん。だろう。」で作業を進めてしまうことがあります。
これを「何故ちゃんと確認しない?」「どれだけ忙しくても、ちゃんと手順を守れ!」
と言っても、実際はそんな余裕が無かったり、焦ったり慌てたり、まぁテンヤワンヤすることもある訳で、
はよせな間に合わんのに、あれもこれも見とられるかっ!( ;゚皿゚)ノシ
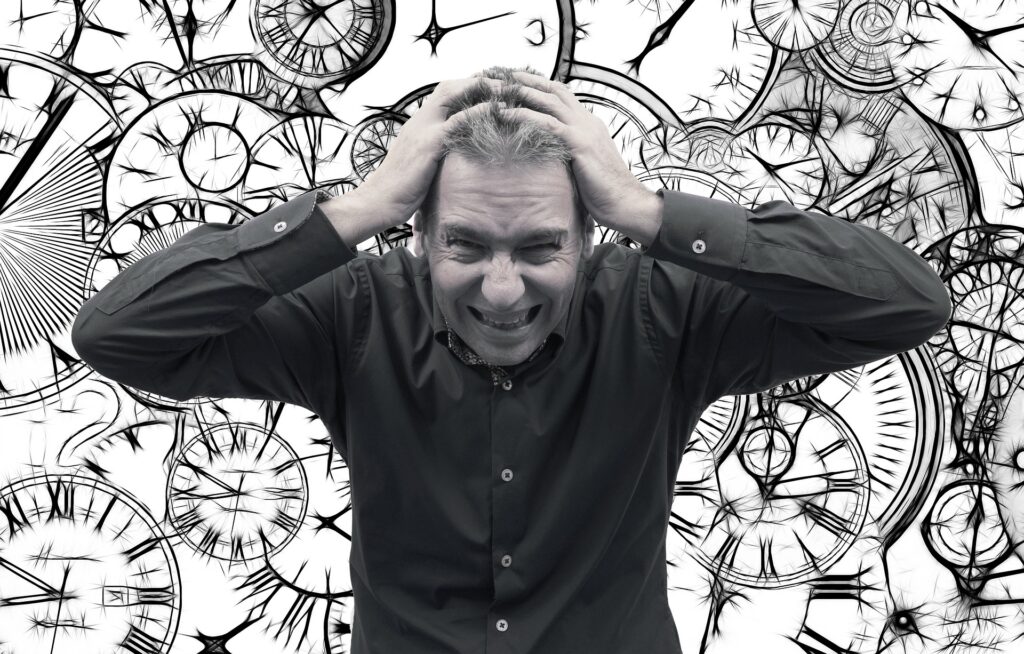
てのが実情でだったりするわけですね(・・;)
工程内で品質を造り込むポイント
では、口頭での注意やマニュアルによる確認だけでは不十分だとなった場合に、どうすれば工程で品質を造り込むのか?
ポイントは
・生産に追われていても確実に品質が確認出来るようにする。
・どんな状況でも確認漏れがない状態をつくる。
・様々な製品の不具合内容を十分理解できている状態にある。
先ほども伝えたように、作業者は時間や能率に追われながら、上記のようなポイントをすべて押さえなければならないということになるわけです。
しかし、現実的にはかなり困難です!
不良品が発生して、
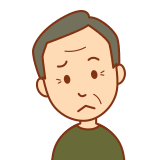
すいません、気を付けてはいたんですが、、、
って、声が聞こえてきます(笑)
現実的な問題
つまり、結論としては
作業者にこれら全てを漏れなく確実に徹底するように!
てのは無理な話し!という事です。
実際現場で品質改善の活動をしていた経験上、そう感じます。
慌ただしい作業の最中に、あらゆる箇所に不具合がないかを確認しつつ、スピーディーに能率良く仕事を捌く!
スーパーマンです(笑)
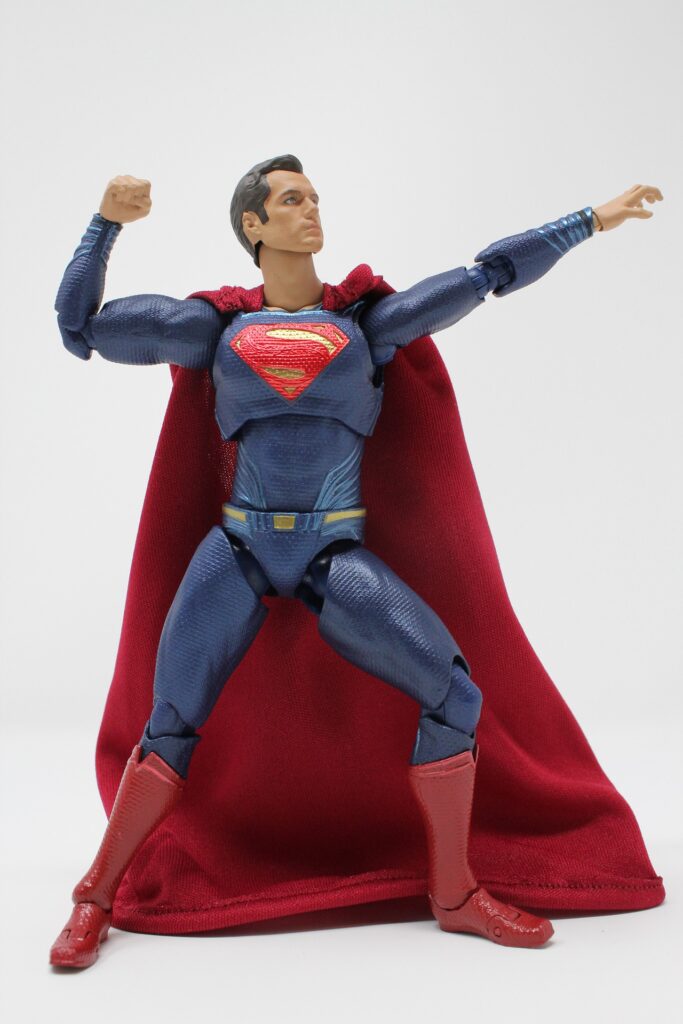
そんな奴、なかなか居ません(T_T)
「速く正確にやってくれ!」
良く聞く言葉ですが、
「はい!わかりました!」なんて言っても、
実際はやろうとしても、どちらも完璧にしっかり両立なんて出来ません(゜ロ゜)
しかも厄介なのが、注意ポイントとして分かっているものなら良いのですが、そうではない場合です。
例えば
- 普段は無いが、たまに発生する不良
- 今まで問題無かったのに、突発で発生した不良
- 問題無しと判断していた事が実は不具合だった
こういったケースですね。
これが本当に厄介!
いつどこに何が出るかわからないのものまで注意しろ!って話ですからね
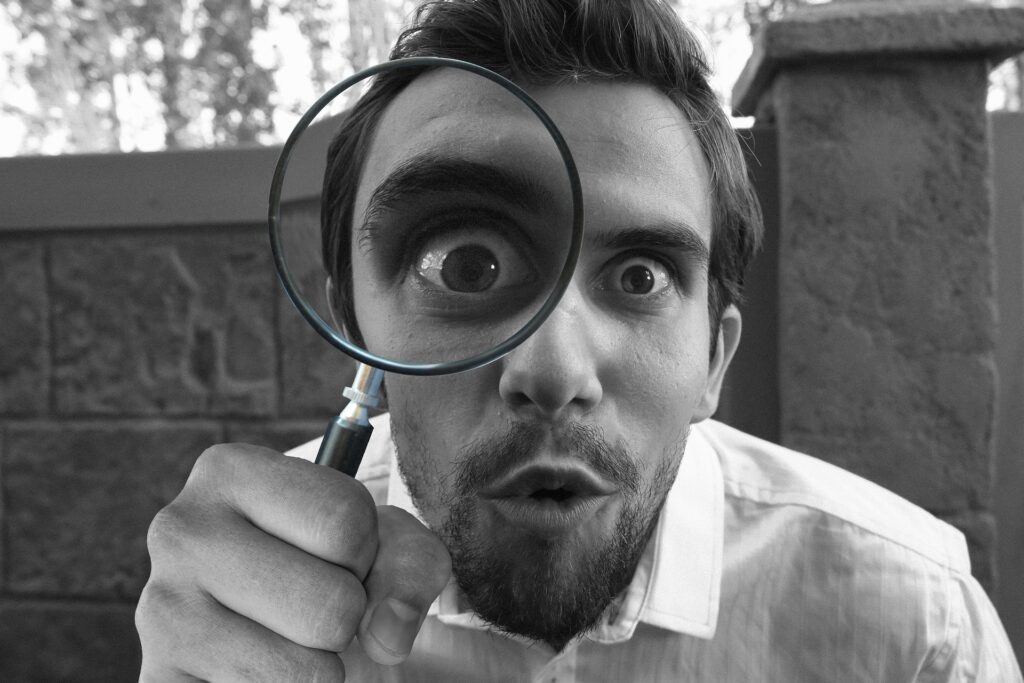
そりゃ時間がいくらでもあるなら見て見てしますよ?
けど、それじゃあ間に合わないですやん?
ということが現実的にはあるわけですね。
『品質を工程で造り込む』ために必要な事
なので
必要な事は
検査員を増員して下流の掃除を頑張って何とかしようとするくらいなら、上流をキレイする活動をしよう!と言うことです。
そこで必要なのが。
『品質担当を配置する!』
と言うことです!
極論ですが、これに限ります!
<具体的な役割は>
・製造工程において、定期的にパトロールを行い品質を確認する
・検査工程での品質情報を把握し、生産工程にフィードバックする
・不具合情報をもとに改善策を検討し、現場に落とし込む
・改善結果をもとにPDCAサイクルを回す
・現場としっかりとコミュニケーションをとり、実態をつかむ
といった役割を持って活動するということです!
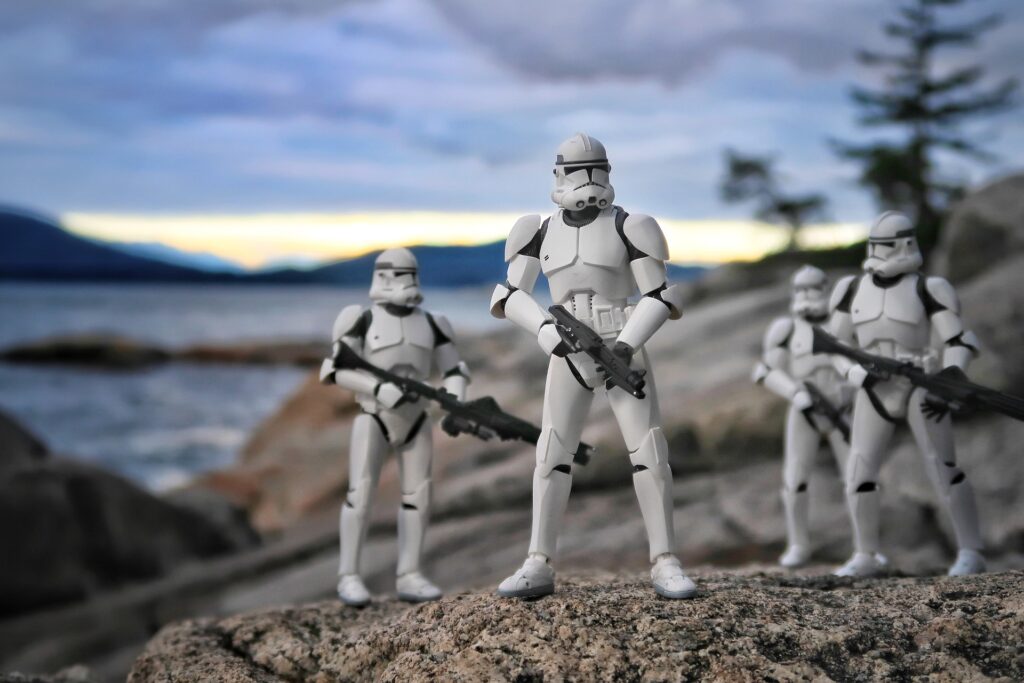
あくまで持論ですが、これが一番確実に『品質を工程で造り込む』ために必要な事だと感じています(^_^)/
特に最後の「現場の実態をつかむ」というのが見落とされがちですが重要です!
なんか、品質管理部門とか品質保証部門的なイメージがしますね♪
この部門がこういった役割を担っても良いし、製造部門にこういった人員を配置しても良いと思います(^.^)
ただし、押さえて置きたいのは『現場は生きている』と言うことです!
ここを見落とすと、活動自体が地に足がつきません!
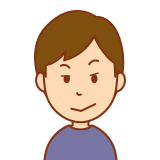
こんなんあったから、気を付けてねー!
と紙だけはって置く。
何てのは良くあることですが、その時だけで終わってしまいます。
貼ってある紙もそのうちボロボロに・・・
これではダメです!
しっかりと、「現場では本当は何が起こっているのか?」と考えながら、根を張って活動することが重要ということです。
そのための具体例なアクションとしては
- 時間や頻度を決めて現場の品質の出来映えをチェックする。
- 検査の品質状況を把握し、良い点も含め現場にフィードバックする。
- 不具合が発生をし対応が必要な時は、現場の作業と一緒なって問題解決をする。
- ただただダメだというのではなく、作業者の声をしっかり聞き、本当の原因を掴む
といったことがたいせつかと思います!
『良い点も含め』というのが『ミソ』ですね♪
製造の現場って、文句は良くいわれるけど褒めてもらえる事は少ないので、一気に信頼性が上がりますよ(^_^)/
まとめ
ということで今回のまとめです。
『品質を工程で造り込む』為に必要な事は
製造部門に品質担当を配置する!
この一点に尽きる!
というのが、私がこれまでやってきた経験上で得た考えですね♪
はじめは、不具合の対応などで検査部門での注力も必要だと思いますが、それだけで終わらず、同時に製造部門での発生を対策していきましょう!
クレーム処理が間に合わないから、不具合が多くて処理しきれないから増員という、場当たり的な考えだけでなく、ここであえて先手を打ちに行きましょう。
検査工程が通常に戻ったら、製造工程の品質担当が常に見回り監視の目を光らせて、不具合発生を未然に防ぐ、あるいは最小限にする活動をつづけます(^_^)/
そうすれば、上流でゴミが発生しなくなり、下流がゴミだらけになることもなく、常にキレイな川が流れるはずです!(笑)
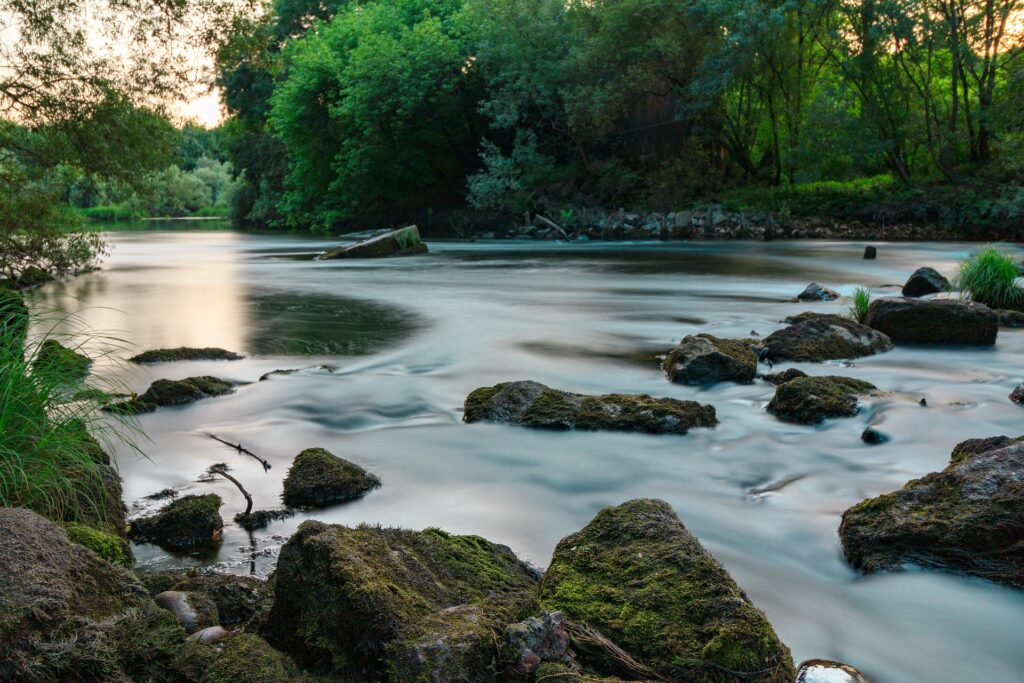
最後まで読んでいただきありがとうございました(^.^)
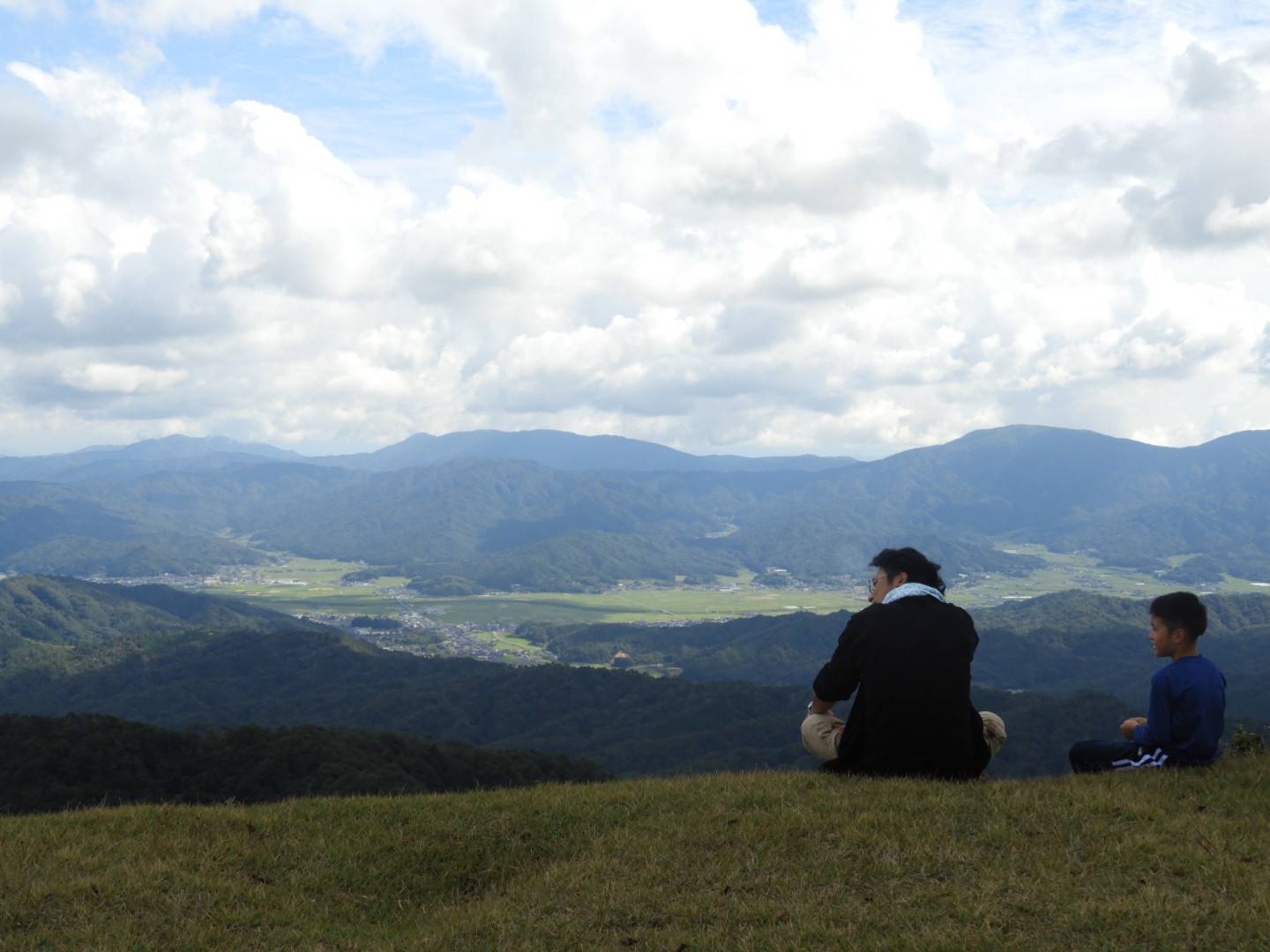
長年の工場勤務にて、管理職として散らかった現場と格闘して、現場改善や効率化、不良・時間外の削減に取り組んできた成果を、ここで発揮出来ればいいな~、と(‘ω’)
どんなことにも興味持ちすぎて、趣味にガンプラ・DIY・etc、色々しすぎて収拾がつかなくなってるかも?(笑)
コメント