前回のおさらい
前回は第2章として『スキルアップ』について取り上げさせてもらいました。
今回は第3章として『作業手順・基準』について取り上げていきたいと思います!
この記事では
・仕事が回らず、残業をしなければならないが、どうしたらうまく回るかわからない。
・会社から経費削減として残業を減らすように言われているがどうしたら良いかわからない。
・いつも帰りが遅く、少しでも早く帰れるようにしたい。
などの課題を抱えている管理職の皆さんに向けて、その解決方法をわかりやすく説明しています。少しでも皆さんの悩みが、この記事を読んで解決すればと思います。
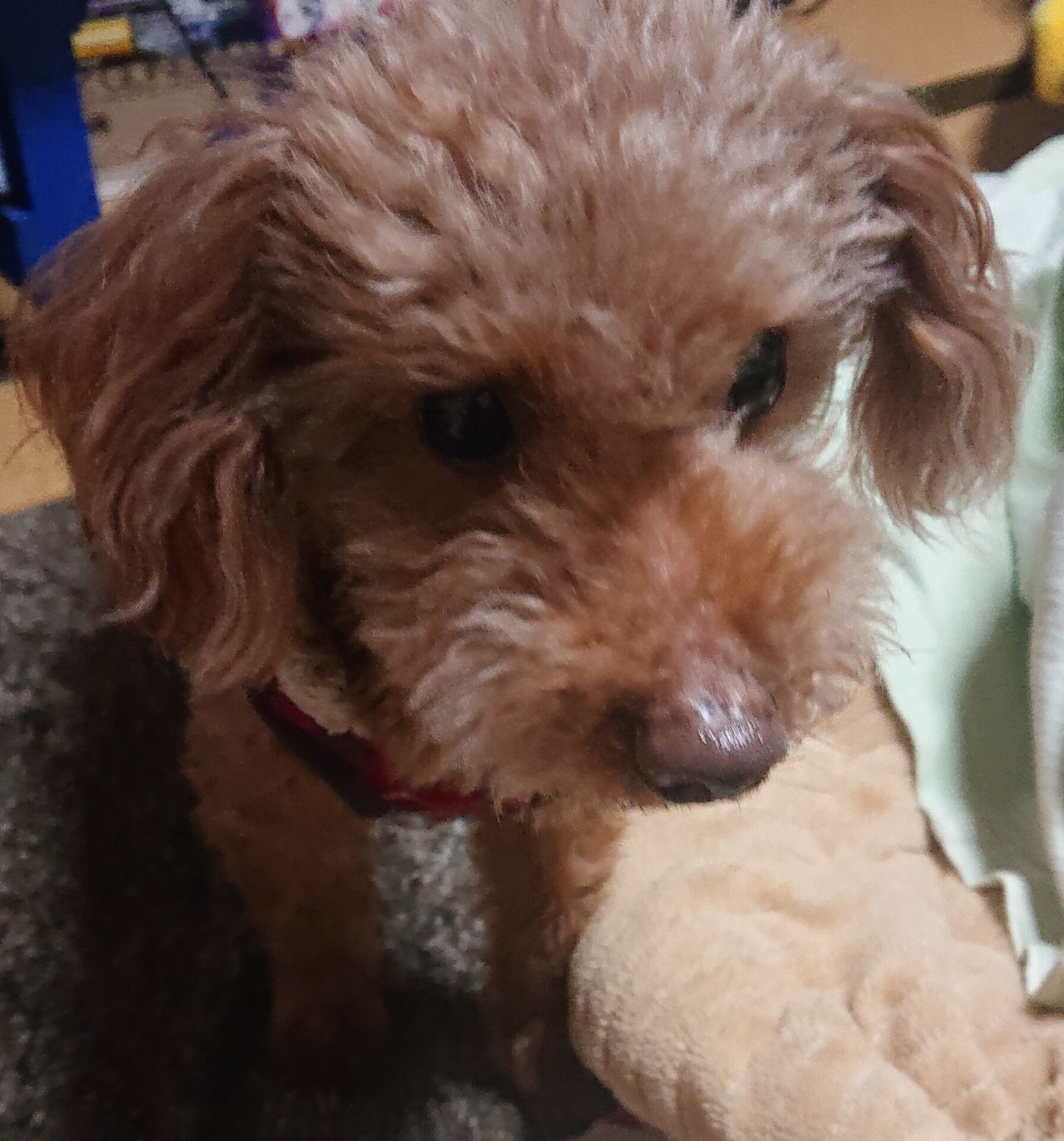
ちなみにこの記事は、10年以上工場勤務をして『現場改善・品質改善』に取り組み、最終的に管理職として組織をマネジメントしてきた経験をもとに書いています。
それでは早速、本題に入りたいと思います(^^)/
作業手順・基準について
作業の手順とは
人によって手順が違う作業ってありませんか?
案外、人によって手順が違ったり、処置の仕方が違ったりで、どれが本当の手順かわからなかったりして悩むことって多いのではないでしょうか?
実はしなくてもいいことに手間かけたりしていて、ふたを空けたら『不必要な作業』だった!
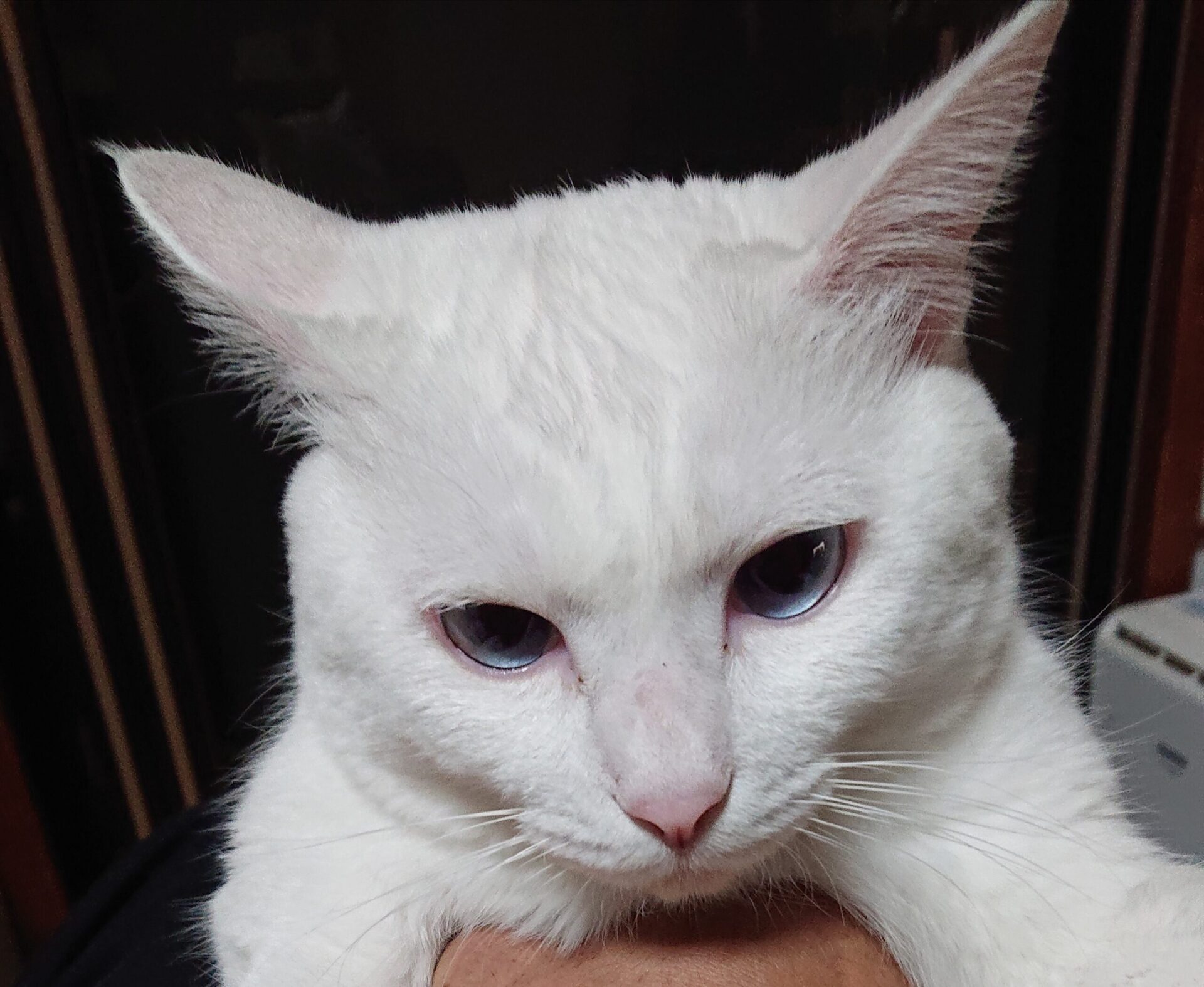
あれ?君何でそんなことしてるん?
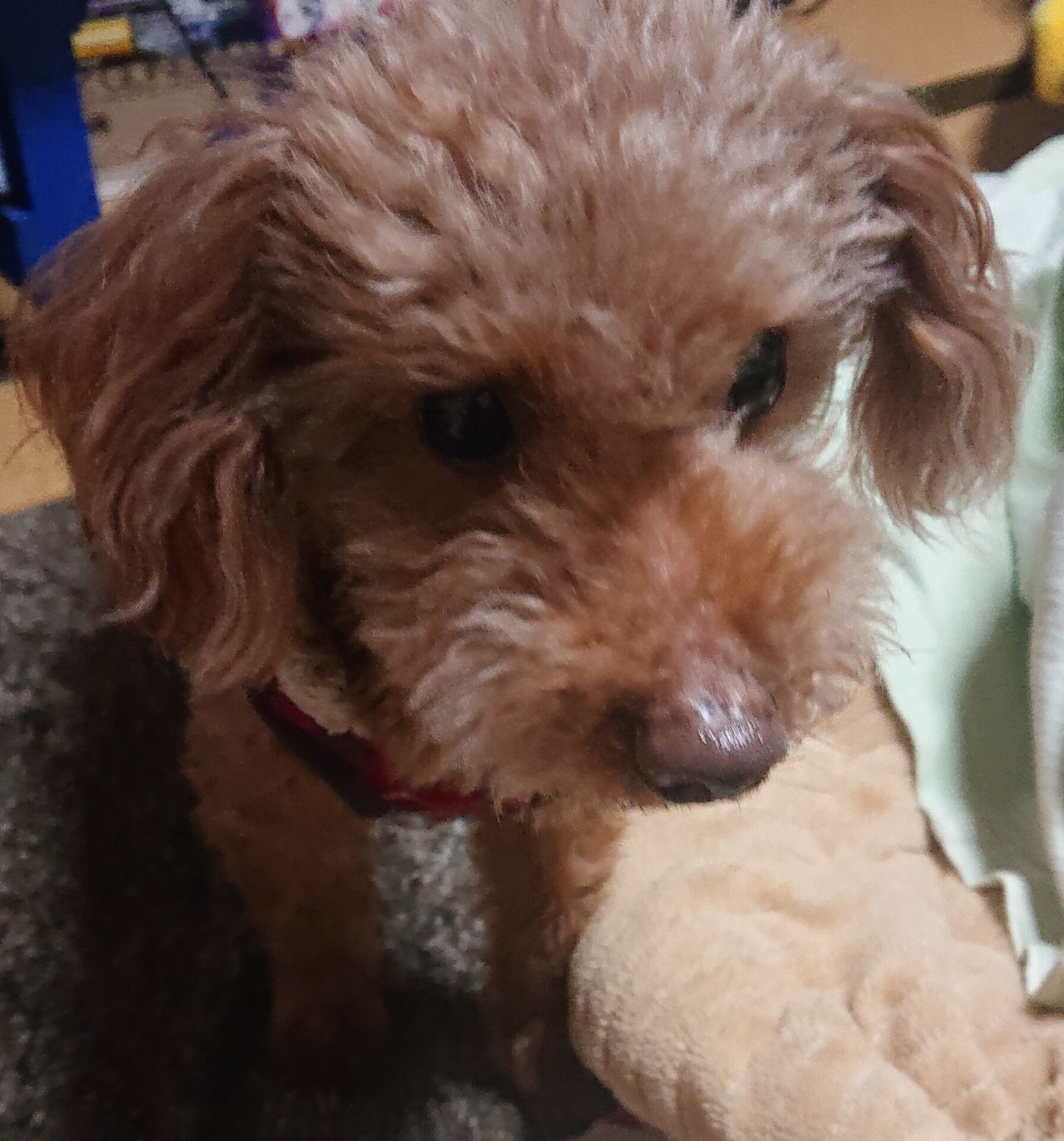
いや、何かこうしろって言われたんで・・・
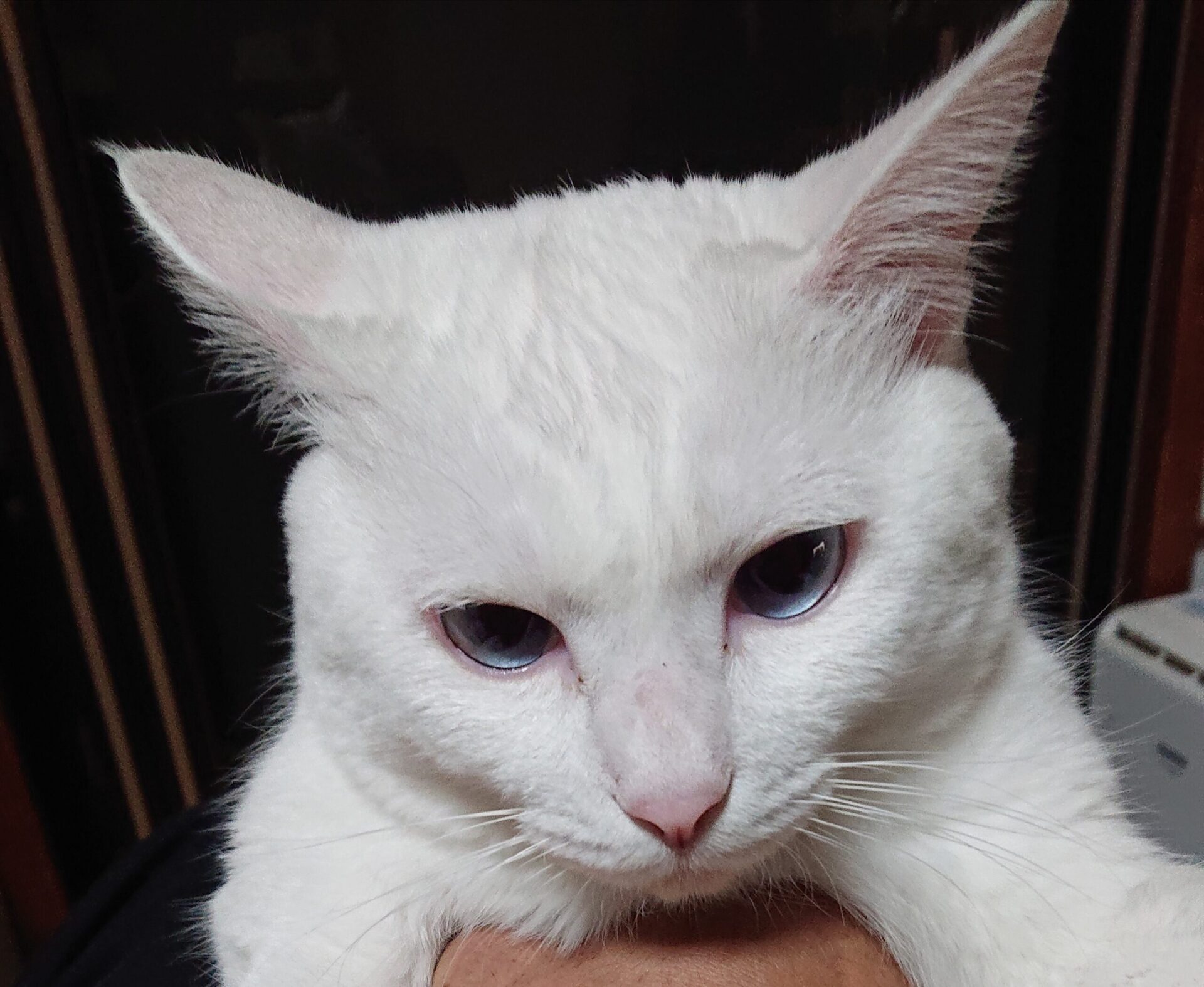
いや、そんな事せんでええし!
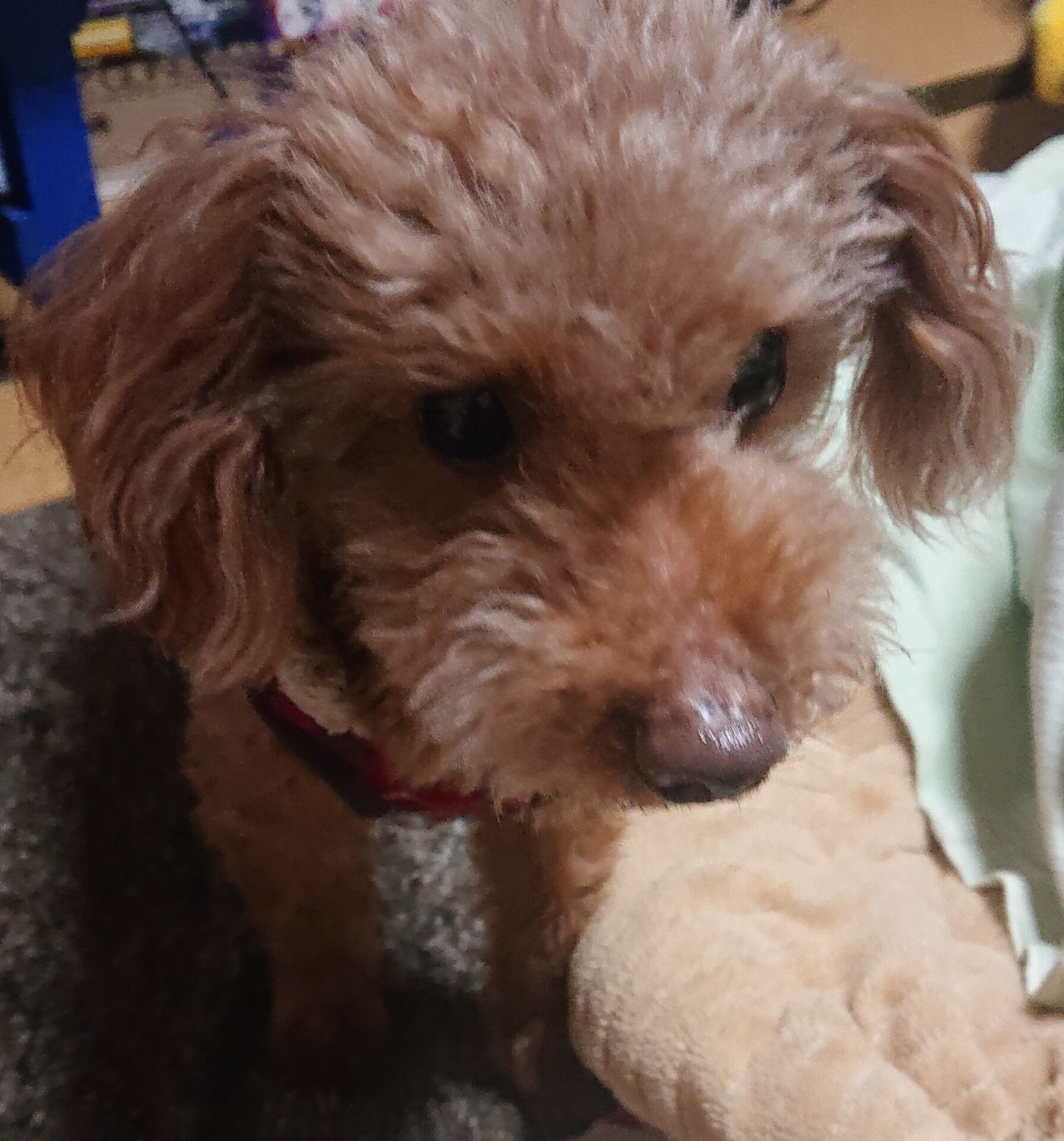
えっ?そうなんですか??
何て事も。
そもそも、本当に必要な作業はなんなのかすらもわからないパターンもあったりするかもしれませんね(・・;)
判断の基準とは
どこまでかOKで、どこからがNGなのかわからない・・・
「まぁまぁこれくらい」つって、人によって「これはいい、これはダメ」などの判断の基準がまちまちになったりするケースですね。
<例えば>
Aさん曰く「これ、あかんから直しといて!」
Bさん曰く「ここは大丈夫だから、なんもせんでええで。」
はて?どっちなん!(@_@)
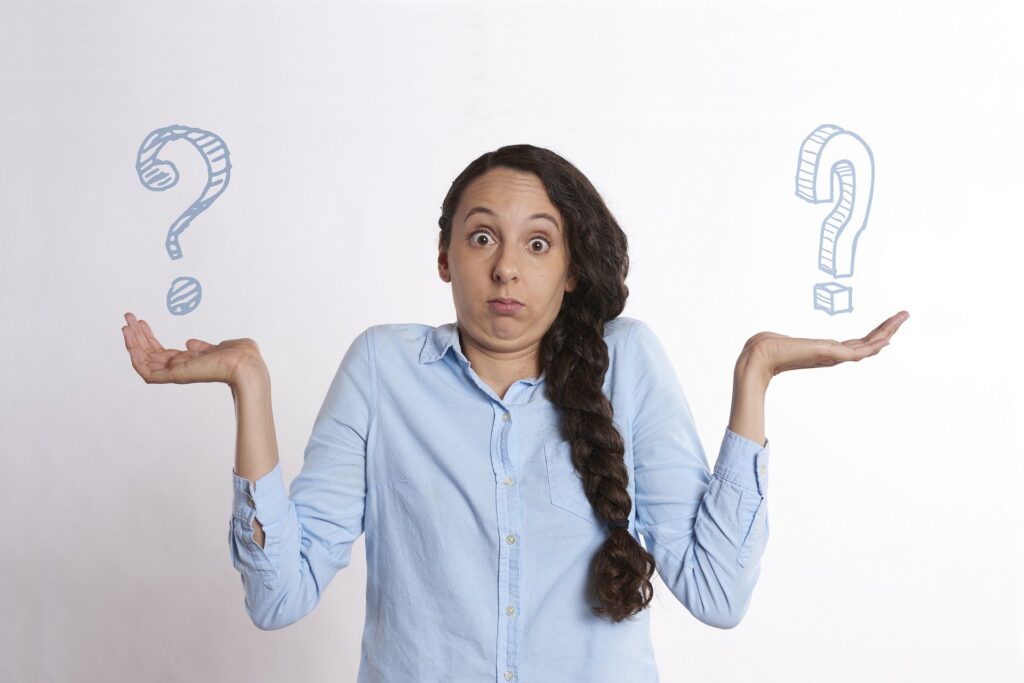
とか言うやつです(笑)
このように、この手順や基準が不明確だとこんなことになったりするわけですね(;’∀’)
手順・基準の不明確だと
先ほども述べたように
- これはどうしたっけ?
- Aさんはこうしてたけど、Bさんはこうしてたし、どっちがホンマ?
- これ位のキズやったらええんちゃう?
- どうなったらダメなんかわからん!
こういった事で作業者は悩み、時間はどんどん消費されていく訳です!
これらの問題を解決することにより、
最終的には『無駄な時間の削減』を図る訳ですね。
そして、結果的に残業時間の削減に繋がっていきます。
では、具体的にどうすれば、こらの問題が解決できるのでしょうか?
具体的な解決策は
作業手順については
例えば
1番効果的なのは、「作業標準書の作成」つまり作業の標準化(マニュアル化)です。
作業標準書とは(wikipediaより)☛https://ja.wikipedia.org/wiki/Standard_Operating_Procedure
要するに『作業の手引書』ってやつですね、例えばですがこんな感じ♪
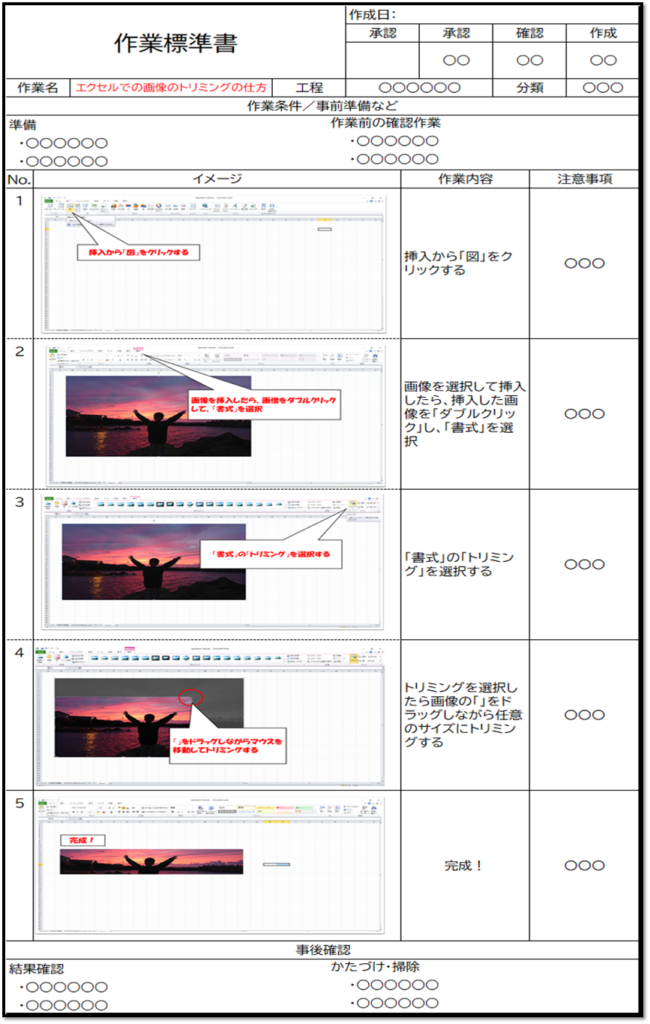
製品ごとに作業手順が明確化されていれば、それにみんなが合わせることで、作業のバラつきが改善されます。
作成した手順やマニュアルはしっかりと写真付きで分かりやすくし、書面化し明示等して作業者がいつでも確認できる状態にしておきます。
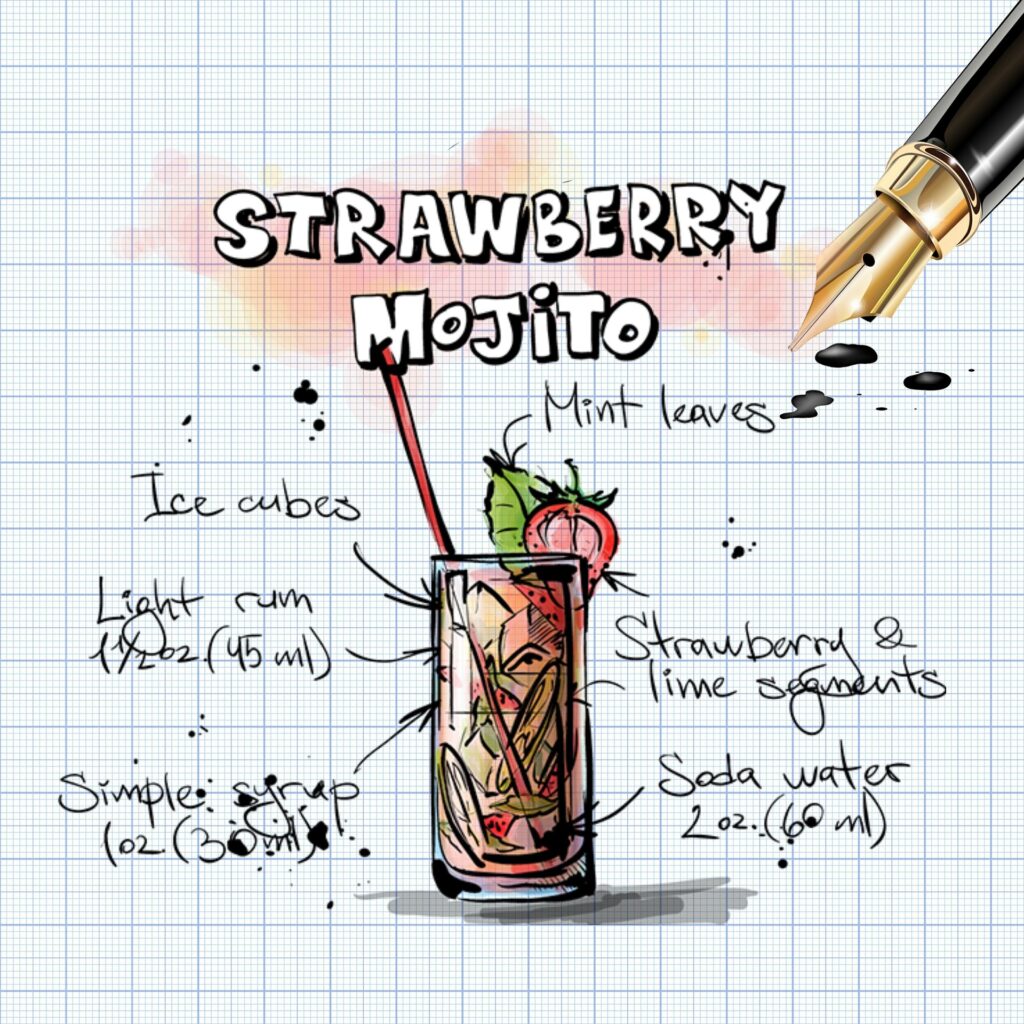
皆やっとることがバラバラ!はこれで解決しますね(^^)/
しかし、全製品をマニュアル化するのはめっちゃ大変なんで、最初は『手順がややこしい製品』や『不具合の多い製品』など的を絞ってやっていくとやり易いと思います(^.^)
判断基準については
良否判断の基準をつくる
不具合があった時に『ん~、とりあえず直そうか』とか何となく感覚で対応していたら、ちょっとした不具合も『実は問題ない』のに、ひたすら手直しをしているなんて状態になって、時間がいくらあっても足らないですよね?
なので、この程度はOK、このレベルはNGという基準をしっかりとつくっておきましょう!
出来る限り、全員が理解しやすいように『数値化』することが望ましいです。
『数値化』すれば普遍的な基準になるので、作業者一人一人が具体的に判断出来ますね♪
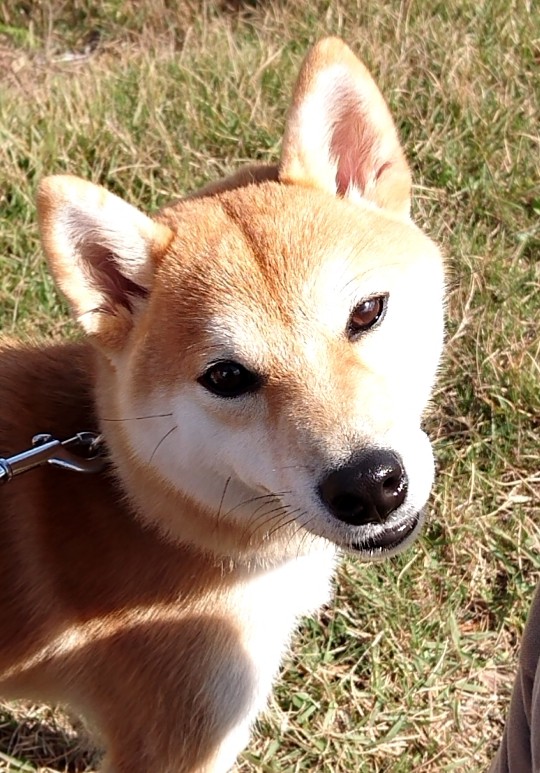
いきなり数値化って、出来るかい!
と思われるかもしれないので、
最初は現場の肌感覚の良否の度合いを確認して、それを数値化していく事を心がけてみると良いと思います!
一旦基準を作ってみて、それを運用してみてどうか?不具合になるようなら見直しをかけていき、『PDCA』サイクルを回していきましょう(^.^)
これもいきなり全製品にというのは大変なんで、『数の多い製品』や『不具合が目玉つ製品』、あるいは 『皆が携わる製品』 など、的を絞って進めていきましょう♪
これは時間のロスの問題もありますが、実は判断する側(管理職やリーダー等)にとっても重要な判断材料になります。
こないだは「OK」と言っていたのに今日は「NG」とか言ってしまうと、現場はかなり混乱してしまいますし、対応がその時その時でマチマチになってしまうと筋が通らなくなって、最悪『話が違う!』とかって信用がなくなったりしますんで(-_-;)
担当者が一人二人くらいなら大きな問題にならないかもしれませんが、皆で手分けしたり携わることが多いような製品では特に注意が必要です!
地道な作業ですがコツコツと進めて、積み上がってくると効果は大きいですよ♪
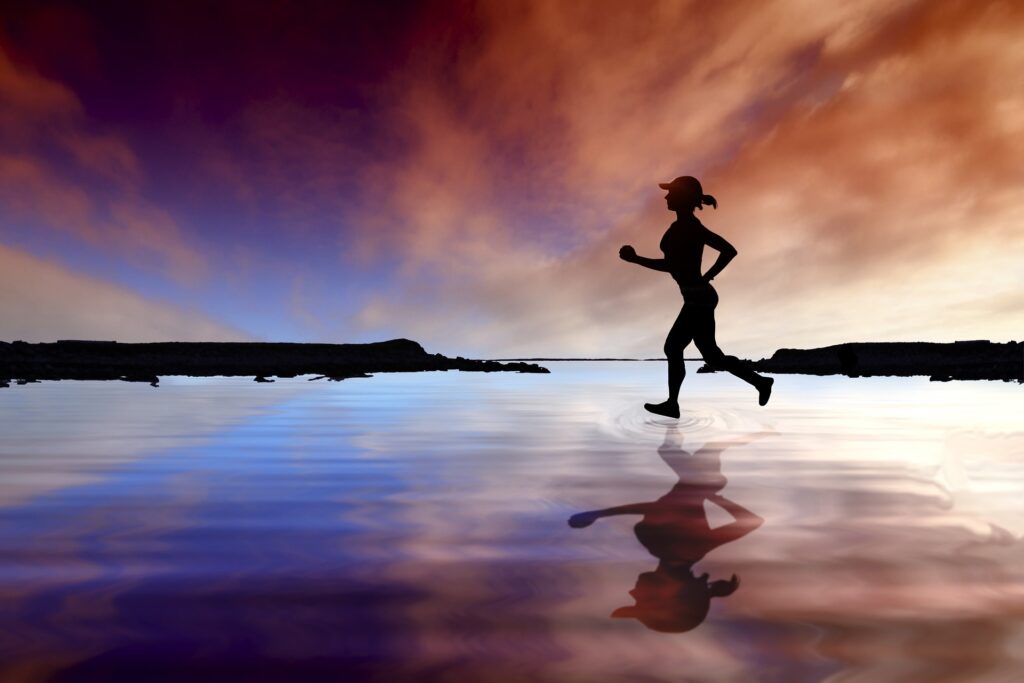
手順・基準を整理することにより効率UP
このようにして、手順・基準を整理することにより作業者の悩む時間が減って判断が早まり、作業効率が上がるというわけです。
作業効率が上がれば、時間の無駄が無くなり、処理しなければならない作業がスムーズに終わります。
そうすれば、時間内に作業が終わり残業の必要が無くなるというわけですね♪
これは、作業者が沢山いればいるほど「人数×」になるので効果的に能率を上げて行けるようになります!
まとめ
どうでしたか?
今回は『手順・基準編』として、作業の手順や基準を整理することによって、結果的に残業が削減出来るようになる。という話でした。
もう一度要点を整理すると
- 作業手順を整理して作業者が悩む時間を削減しよう!
- どこまで良いかダメかを明確にして、作業者が悩む時間を削減しよう!
つまり『作業者が悩む時間』がポイント!ということです。
『作業者が悩む時間』というのは良くあることで、案外ピックアップされにくいですが、わずかな時間でもそれが集まればそれなりにまとまった時間になります。
『チリも積もれば山となる』じゃないですが結果的に多くの時間を使っているわけですね♪
これをいかに減らすか?
が、今回の『手順・基準編』の大きなネライということです!
無駄な作業を少しでもなくし、悩む時間を最小限にして、効率よく作業を進めていこう!ということです♪
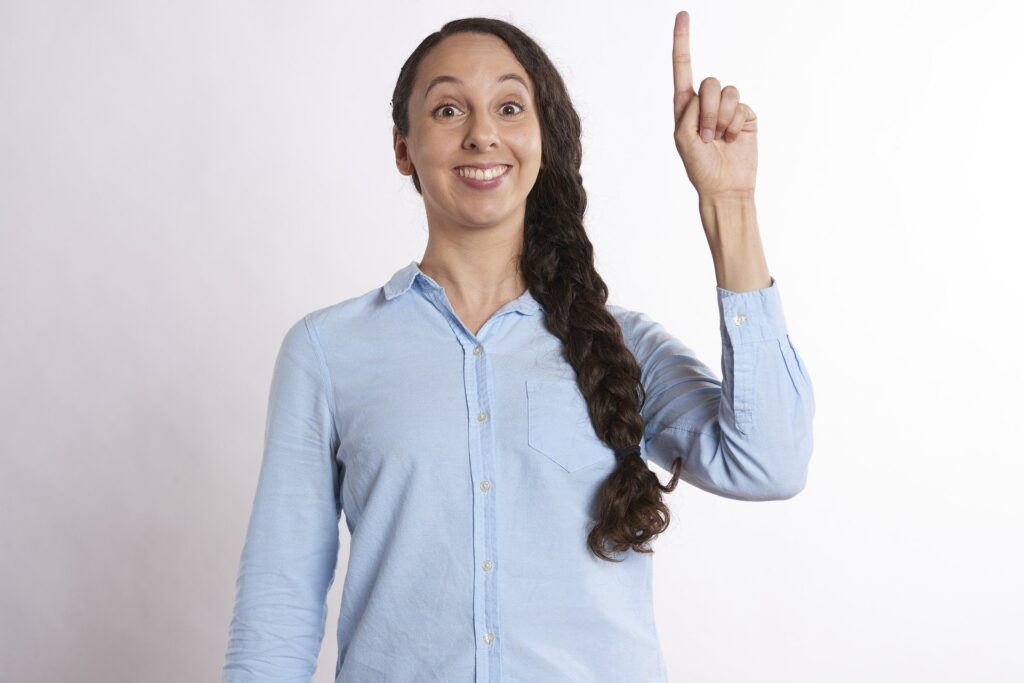
ということで、第3章は『作業基準・手順』について取り上げさせてもらいました!
次回、最後の章としてこれまでのまとめをして、今回の『残業時間の削減』についての記事を終わりにしたいと思います♪
最後まで読んでいただきありがとうございました(=゚ω゚)ノ
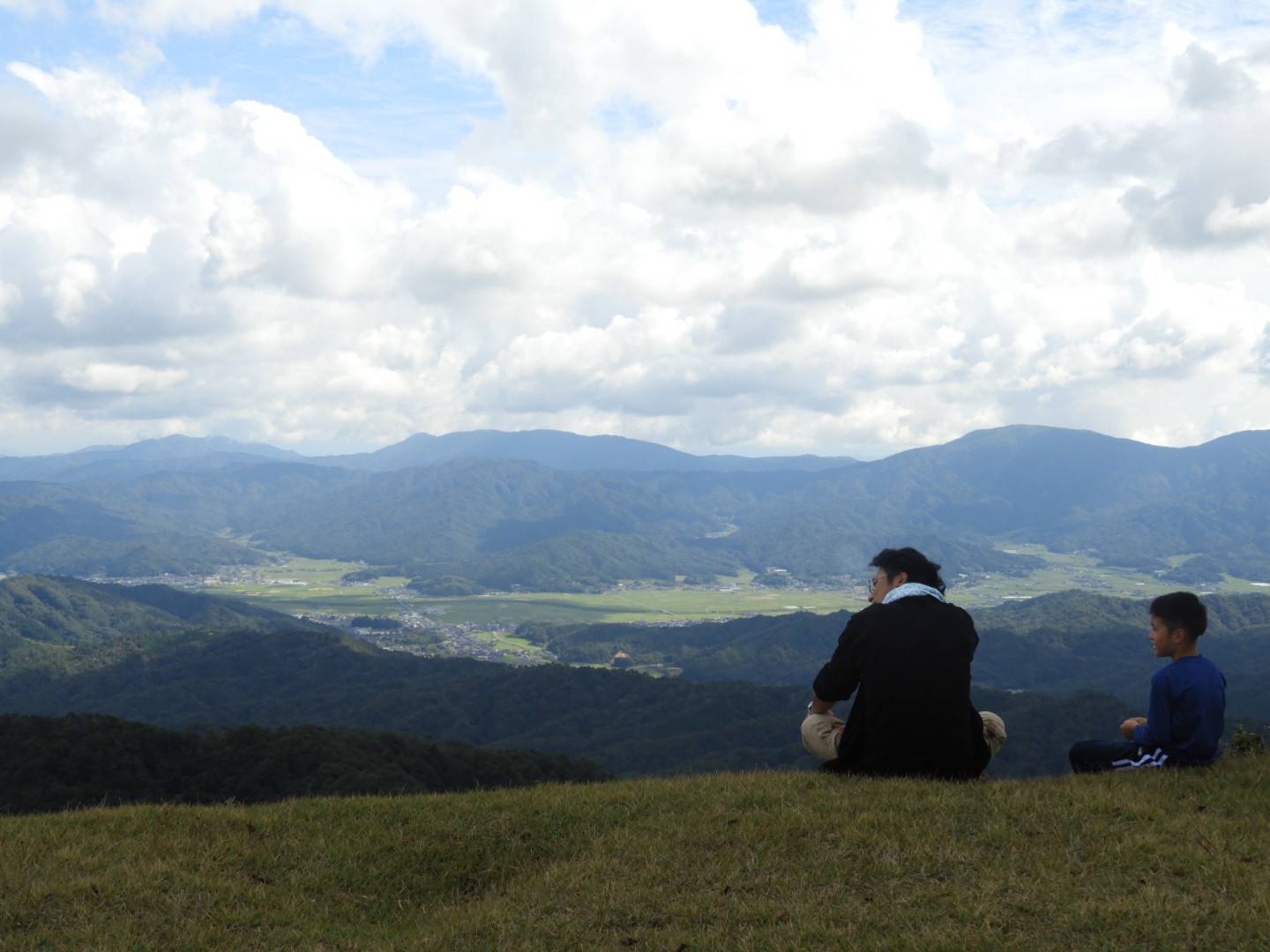
長年の工場勤務にて、管理職として散らかった現場と格闘して、現場改善や効率化、不良・時間外の削減に取り組んできた成果を、ここで発揮出来ればいいな~、と(‘ω’)
どんなことにも興味持ちすぎて、趣味にガンプラ・DIY・etc、色々しすぎて収拾がつかなくなってるかも?(笑)
コメント